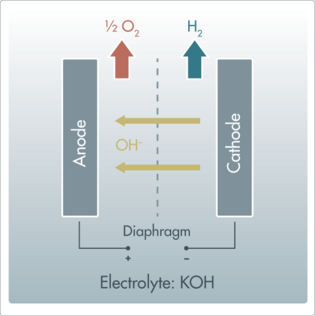
Alkaline electrolysis is used to separate hydrogen from water. The electrolysis cell comprises an anode chamber and a cathode chamber separated by a thin porous diaphragm. The metal electrodes are located at a small distance from the diaphragm, immersed in an aqueous alkaline solution. When a voltage is applied, hydroxide ions (OH−) and hydrogen gas (H2) are produced at the cathode. The negatively charged hydroxide ions move through the diaphragm from the cathode to the anode where oxygen gas (O2) and water are produced:
Cathode reaction: | 2 H2O + 2 e– → 2 OH– + H2 |
Anode reaction: | 2 OH– → ½ O2 + H2O + 2 e– |
Total reaction: | H2O → H2 + ½ O2 |
Benefits of alkaline electrolysis include a long durability and high plant performance. Based on the operating principle, water is introduced at the cathode using the alkaline electrolyte circuit. Usually, alkaline electrolysis occurs at temperatures from 60 to 90 °C and at stack pressures slightly above atmospheric pressure, or when pressurized, at up to 30 bar.

Hydrogen separation and conditioning
Exact combined control of the pressure and gas flow of the hydrogen produced in the electrolysis stack is essential: it must be sized in line with the desired wide performance spectrum of the electrolyzer to cover a wide gas range. Additionally, the applied valves must fulfill the strictest requirements concerning seat leakage and fugitive emissions and be rugged to handle liquids contained in the gas flow. For small to medium gas flow rates, globe valves have proven to be a viable solution while rotary plug valves are better suited to deal with high gas flow rates. Suitable valve types from the SAMSON portfolio include: SAMSON Type 3510, Type 3252, Type 3241, SAMSON VETEC Type 82.7 etc. Butterfly valves are a good option for (additional) shut-off features, ball valves for small nominal pipe sizes.

Oxygen separation and conditioning
Exact combined control of the pressure and gas flow is also essential for handling the oxygen produced in the electrolysis stack: it must be sized in line with the desired wide performance spectrum of the electrolyzer to cover a wide gas range, particularly when using the produced oxygen. All materials must be compliant with the specifications applicable to use in oxygen service. Additionally, the applied valves must fulfill the strictest requirements concerning seat leakage and fugitive emissions and be rugged to handle liquids contained in the gas flow. For small to medium gas flow rates, globe valves have proven to be a viable solution while rotary plug valves are better suited to deal with high gas flow rates. Suitable valve types from the SAMSON portfolio include: SAMSON Type 3510, Type 3252, Type 3241, SAMSON VETEC Type 82.7 etc. Butterfly valves are a good option for (additional) shut-off features, ball valves for small nominal pipe sizes.

Water treatment
Deionized water is needed as the basis for providing the required alkaline electrolyte. The associated process calls for an optimized selection of valve materials to guarantee ruggedness in operation and a long service life. Suitable valve types from the SAMSON portfolio include: SAMSON Type 3241, Type 3244, SAMSON SED Type 58x, SAMSON PFEIFFER Type 26d, Type 1b etc.

Electrolyte circuit
Water is mixed with hydroxide to form an aqueous alkaline solution that supplies ionic conductivity. Depending on the alkaline parameters (such as concentration, temperature), the valves are selected with a high-quality (PTFE or PFA) lining or made of suitable stainless steels. Suitable valve types from the SAMSON portfolio include: SAMSON PFEIFFER Type 10e, Type 20a, Type 20b, Type 1a, Type 1b, SAMSON Type 3241, Type 3244 etc.

Cooling systems
The heat produced during the electrolysis process is discharged over cooling systems and supplied to other heat consumers. Excess heat must also be dissipated from the alkaline electrolyte circuit. Suitable valve solutions to ensure precise control at partly high flow rates of the cooling agents include globe and rotary valves with high flow coefficients. Suitable valve types from the SAMSON portfolio include: SAMSON Type 3241, Type 3244, Type 3321, Type 3323, SAMSON PFEIFFER Type 11e, Type 10e, Type 14b etc.

Nitrogen control
In the electrolyzer, nitrogen is used for inertization and certain purification processes. For nitrogen handling, automated control valves or self-operated regulators are used that can ensure exact control and at the same time minimize nitrogen consumption. Suitable valve types from the SAMSON portfolio include: SAMSON Type 44-x, Type 2405, Type 41-23, Type 3510, Type 3252, Type 3241 etc.
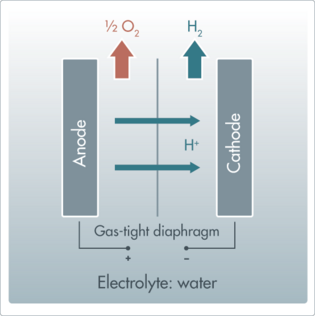
PEM (Proton Exchange Membrane or Polymer Electrolyte Membrane) electrolysis is a process to produce hydrogen from water. In the electrolysis cell, a conductive proton exchange membrane is immersed in water. When a voltage is applied, oxygen gas (O2) and hydrogen ions (H+) are produced. The positively charged hydrogen ions move through the membrane from the anode to the cathode where hydrogen gas (H2) is produced:
Anode reaction: | H2O → ½ O2 + 2H+ + 2 e– |
Cathode reaction: | 2 H + 2 e– → H2 |
Total reaction: | H2O → H2 + ½ O2 |
PEM electrolysis is capable of handling severe load fluctuations, which means that the process can respond very quickly to fluctuations in the power supply. Fundamentally, PEM electrolysis is compact in its design with the water being introduced directly at the anode. PEM electrolysis usually occurs at temperatures from 50 to 80 °C. While the anode is basically pressureless, the cathode can also be operated at high pressures (typically up to 50 bar with the possibility and target of up to 350 bar). This helps reduce the amount of energy later needed to condense the hydrogen for transport and storage.

Hydrogen separation and conditioning
Exact combined control of the pressure and gas flow of the hydrogen produced in the electrolysis stack is essential: it must be sized in line with the desired wide performance spectrum of the electrolyzer to cover a wide gas range. Additionally, the applied valves must fulfill the strictest requirements concerning seat leakage and fugitive emissions and be rugged to handle liquids contained in the gas flow. For small to medium gas flow rates, globe valves have proven to be a viable solution while rotary plug valves are better suited to deal with high gas flow rates. Suitable valve types from the SAMSON portfolio include: SAMSON Type 3510, Type 3252, Type 3241, SAMSON VETEC Type 82.7 etc.

Oxygen separation and conditioning
Exact combined control of the pressure and gas flow is also essential for handling the oxygen produced in the electrolysis stack: it must be sized in line with the desired wide performance spectrum of the electrolyzer to cover a wide product gas range, particularly when using the produced oxygen. All materials must be compliant with the specifications applicable to use in oxygen service. Additionally, the applied valves must fulfill the strictest requirements concerning seat leakage and fugitive emissions and be rugged to handle liquids contained in the gas flow. For small to medium gas flow rates, globe valves have proven to be a viable solution while rotary plug valves are better suited to deal with high gas flow rates. Suitable valve types from the SAMSON portfolio include: SAMSON Type 3510, Type 3252, Type 3241, SAMSON VETEC Type 82.7 etc. Butterfly valves are a good option for (additional) shut-off features, ball valves for small nominal pipe sizes.

Water treatment
Deionized water is needed as the basis for the PEM electrolysis. The associated process calls for an optimized selection of valve materials to guarantee ruggedness in operation and a long service life. Suitable valve types from the SAMSON portfolio include: SAMSON Type 3241, Type 3244, SAMSON SED Type 58x, SAMSON PFEIFFER Type 26d, Type 1b etc.

Cooling systems
The heat produced during the electrolysis process is discharged over cooling systems and supplied to other heat consumers. Excess heat must also be dissipated from the alkaline electrolyte circuit. Suitable valve solutions to ensure precise control at partly high flow rates of the cooling agents include globe and rotary valves with high flow coefficients. Suitable valve types from the SAMSON portfolio include: SAMSON Type 3241, Type 3244, Type 3321, Type 3323, SAMSON PFEIFFER Type 11e, Type 10e, Type 14b etc.

Nitrogen control
In the electrolyzer, nitrogen is used for inertization and certain purification processes. For nitrogen handling, automated control valves or self-operated regulators are used that can ensure exact control and at the same time minimize nitrogen consumption. Suitable valve types from the SAMSON portfolio include: SAMSON Type 44-x, Type 2405, Type 41-23, Type 3510, Type 3252, Type 3241 etc.