Pressure Swing Adsorption
Reliable control at all stages in the process
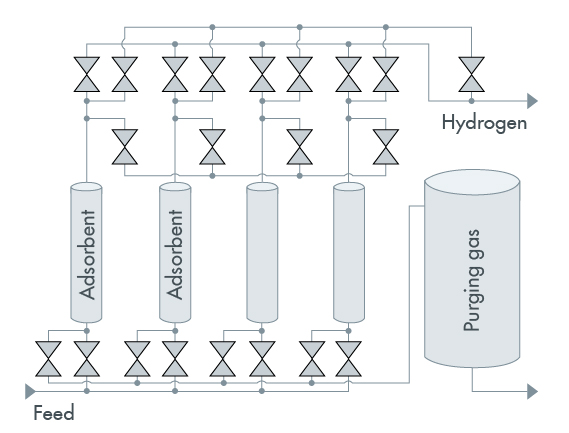
Pressure swing adsorption is a process that separates single gases from a gas mixture. It is mainly used in chemical and petrochemical processes as well as the steel industry, for example to recover hydrogen (H2) from coking or conversion gases, or to separate oxygen (O2) and nitrogen (N2) from air.
The adsorption process is based on gas molecules binding to an adsorbent material. The adsorbent bed is specially selected depending on the gas to be adsorbed. Ideally, only the gas to be separated is adsorbed, while all other gases in the mixture pass through the adsorbent bed. Frequently, adsorbents containing carbon (e.g. activated carbon or carbon molecular sieves) and oxide adsorbents (e.g. zeolite) are used. The purity of the adsorbed gas not only depends on the adsorbent used. The temperature and pressure during the process are important as well. As a result, the control valves used also contribute considerably to the quality of the end product.
The pressure swing adsorption process is divided into four stages that occur in cycles:

Adsorption: adsorption takes place at high pressure (up to 40 bar). The feed gas is fed through an adsorbent bed. The adsorbent binds the easily adsorbable gas molecules, while gas molecules that are not readily adsorbable or not adsorbable at all pass through the bed. The adsorbent bed continues to adsorb gas molecules until it reaches its full capacity.
Suitable valves
- Reliability even at extremely high number of cycles
- Long service life
- Proven in use
- Product purity throughout the entire process
- Fugitive emission requirements verified in tests before product launch
- Ruggedness despite high mechanical load (frequent load changes)
- Easy maintenance
- Flexible upgrading through proven modular design
- Bi-directional flow (valve and flow divider)